In the modern digital age, IT has become an integral part of the manufacturing process, transforming traditional factories into smart and efficient production centers. Today, manufacturers rely on advanced technical solutions to improve productivity, ensure quality, and reduce costs. This is from the use of integrated systems to manage industrial processes to IoT applications and massive analytics. It therefore plays a critical role in enhancing performance and streamlining processes. In this article, we will look at the most important IT solutions in manufacturing, and together we will discover how these innovations contribute to a comprehensive digital transformation that increases companies’ competitiveness in the global market.
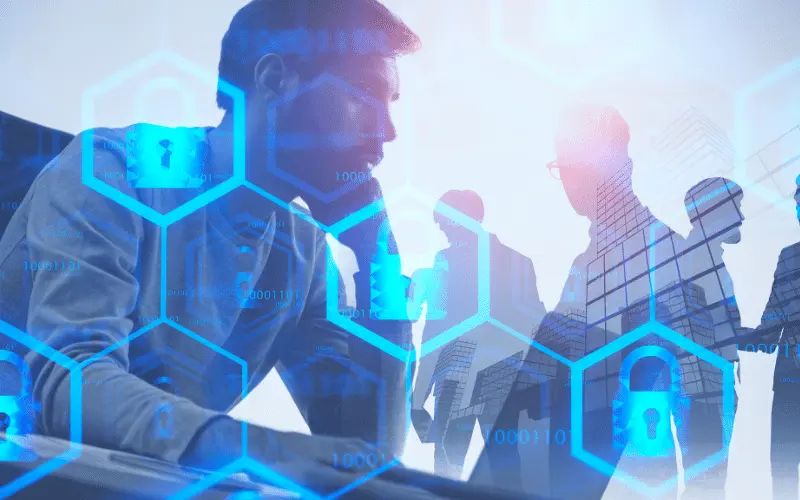
Definition of IT solutions in manufacturing
They are defined as a set of techniques and programs specifically designed to help manufacturing companies improve their operations and increase productivity and manufacturing efficiency. These solutions include a wide range of technical tools and solutions that are in the industry’s interest.
The most important IT solutions in manufacturing
1. Digitization & Industry 4.0
Industry 4.0 or the Fourth Industrial Revolution is one of the most important digital developments in industry. This concept combines advanced technologies such as the IOT (Internet of Things), cloud computing, artificial intelligence, and other modern technological innovations to serve different manufacturing processes. These include the transformation of manufacturing processes and functions from physical to digital. Thus, the Fourth Industrial Revolution allows the analysis of an enormous amount of data in real-time, helping manufacturers to discover important information about the course of their industrial process. It also contributes to product quality forecasting, maintenance, etc.
2. Digital Twins
Digital תאום is a precise default model for a physical object or system, such as a factory or machine. It is created using data from the real world, such as sensors, and is constantly updated to reflect the state of its physical counterpart. In other words, it is a digital replica that simulates the physical object in real-time. In factories, digital twins play an important role in improving production. By monitoring performance, predicting maintenance, and designing new products.
3. Robots and Automation
Robotics and automation are some of the most important IT solutions that have greatly improved production quality through three main points: reducing labor costs, reducing the time needed for different production processes, improving production quality, and easily identifying damaged parts. Robots have thus contributed significantly to the production process by taking on dangerous tasks that may threaten human life when performed such as welding, shearing, assembling materials, etc.
4. Extended Reality
Extended reality refers to technologies that integrate reality with the virtual world. The extended reality enables the creation of virtual industrial models and the testing of their impact. It also plays a significant role in the staff training process. In addition, it contributes to improved product design by testing their virtual models before the manufacturing process. It can also enhance customer experience by offering product demonstrations before buying them.
5. Artificial Intelligence (AI) Solutions
The power of artificial intelligence lies in its ability to handle a huge amount of data, and then detect patterns, and predict outputs. Thus, artificial intelligence can collect data from industrial equipment through IIOT sensors. Then process this data and analyze its patterns to determine the procedures to be followed to improve the production process. In addition, machine learning algorithms embedded in AI help identify abnormal patterns in the manufacturing process. Thus facilitating the identification and disposal of defective outputs to improve production efficiency. Through its predictive capabilities, AI can manage and identify risks in advance. Contributing to a clear plan to avoid negative consequences if they occur.
6. Industrial Internet of Things (IIOT)
It is a network of embedded devices, such as sensors, transponders, and computers. Connected to the Internet to collect and exchange data. In the manufacturing environment, IIOT is used to monitor and improve processes. Enhance manufacturing efficiency, reduce costs, and improve product quality. This technology can monitor operations in real-time, forecasting breakdowns to reduce costs for repair. They also contribute to increasing safety by assessing potential risks in manufacturing processes and innovating new services and products.
7. 3D printing
It is known as additional manufacturing (AM) or rapid prototyping. It is a technique based on the creation of physical 3D models from a digital model. They also build the layers of the model and twist the other, allowing for more complex designs. Thus, they allow for the creation of low-cost models for pre-testing in the manufacturing process. They can also be used to manufacture products locally, reducing freight costs, and improving supply chains.
8. Cloud Computing
They are a model for providing IT services, such as servers, storage, networks, software, and online. Instead of buying, building, and maintaining infrastructure, they can be rented from a cloud service provider such as Amazon Web Services (AWS), Microsoft Azure, or Google Cloud Platform (GCP). Cloud computing reduces continuous operating costs, and eliminates the need to purchase software, and maintain hardware. They also provide access to an enormous amount of computer resources allowing companies to expand rapidly. They also protect data when disasters occur because they will be kept in a virtual space rather than local preservation on a device or hard drive. It facilitates the exchange of files between staff.
Benefits of IT solutions in the industrial field
· Increased productivity
IT and its effective solutions help manufacturing companies automate recurring tasks, improve the efficiency of completed processes, and reduce the time needed to complete them. This increases productivity significantly.
· Improved Product Quality
It can help companies better monitor product quality, improve manufacturing processes, and make them more accurate. In addition to early detection of defects, this helps improve product quality and reduce losses.
· Cost Reduction
Technology can help reduce raw resource costs. This is done by accurately estimating the quantity of materials needed for the manufacturing process and improving the storage conditions of these materials, thereby reducing material losses resulting from damage.